The same care must be taken in the design and implementation of these five contacts.
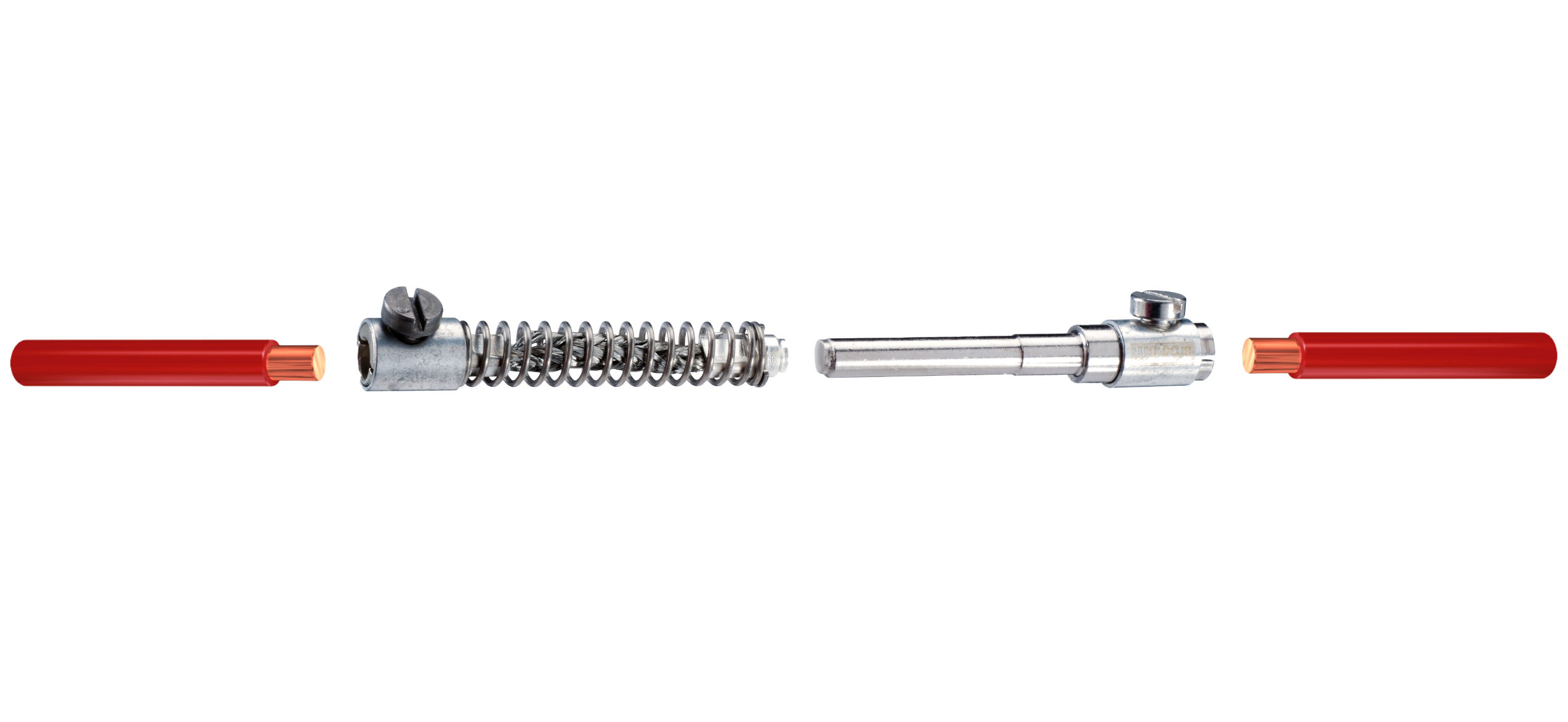
1. The contact of the conductor in the clamp of the plug socket-outlet.
2. and 3. The crimps at the 2 ends of the braid.
4. The contact at the socket/plug interface.
5. The conductor contact in the plug clamp.