High-performance, long-lasting technical materials
to suit every application
Our equipment in POLYESTER
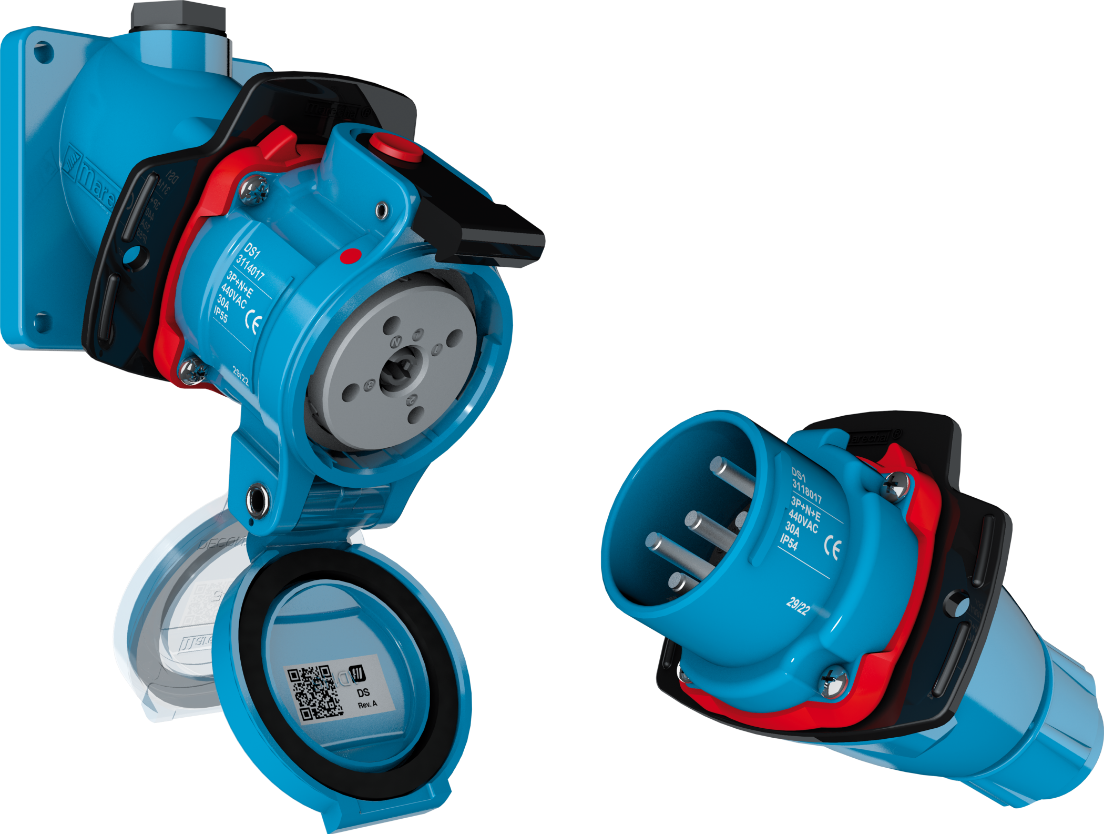
Glass-fibre reinforced polyamide (GRP)
Glass-fibre reinforced polyamide (GRP) is a material that combines the properties of polyamide with the benefits of glass fibre reinforcement. Here are some of the typical properties of GRP:
-
Excellent mechanical resistance
Glass-fibre reinforcement gives polyamide superior mechanical strength, particularly in terms of impact and abrasion resistance, tensile strength, flexural strength and compressive strength. Industrial socket outlets can be exposed to harsh working conditions. GRP is a robust material suitable for a wide range of applications, reducing replacement and maintenance costs over the long term.
-
Lightweight
Although GRP is very resistant, it remains relatively light compared to other materials, making it easier to install and handle industrial plug socket-outlets for applications requiring both strength and lightness.
-
Corrosion resistance
GRP is naturally resistant to corrosion, making it a wise choice in corrosive or humid environments where other materials may deteriorate more quickly.
-
High levels of electrical insulation
Good electrical insulation is essential for user safety and protection against short circuits.
-
Resistance to extreme temperatures
GRP can withstand both low and high temperatures, allowing it to be used in environments ranging from [-40°C to +60°C] without any special precautions. GRP also has a low coefficient of thermal expansion, which means it retains its shape and dimensions over a wide range of temperatures.
-
UV resistance (f1)
If industrial plug socket-outlets are used outdoors or in environments exposed to UV rays, it is important that the material is resistant to degradation caused by prolonged exposure to sunlight.
GRP retains its mechanical properties and colour even under prolonged UV exposure, making it ideal for outdoor use. -
Chemical resistance
In certain industrial environments, plug socket-outlets may be exposed to aggressive chemicals and cleaning agents. GRP is resistant to many chemicals, making it an appropriate choice for these applications.
-
Ease of manufacture
GRP can be moulded into a variety of complex shapes, allowing the industrial plug socket-outlets to meet the specific needs of each application.
These properties make glass fibre reinforced polyamide a robust and versatile choice for industrial plug and socket-outlets, offering strength, longevity, and electrical safety.
Our metal equipment
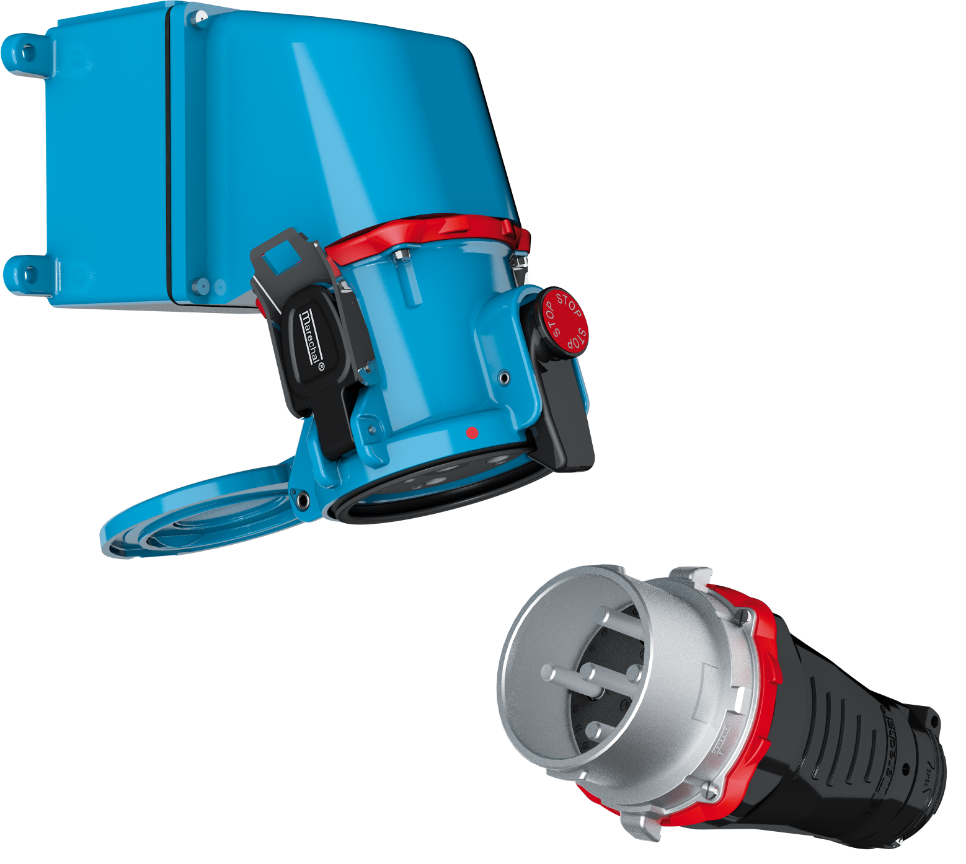
Zamak
Zamak is an alloy of zinc, aluminium, magnesium and copper. Zamak has a relatively low melting point compared with other metals and is easy to machine, which facilitates the manufacturing process and allows complex shapes to be produced with extremely fine details and thicknesses. The surface appearance depends on the moulding and the finish: rough, paint, or coated against corrosion.
-
Excellent mechanical resistance
Zamak offers great mechanical strength, which is crucial for industrial plug socket-outlets that may be subjected to significant stress during use. Good tensile strength, impact resistance and wear resistance. Good damping capacity. Good dimensional stability.
-
Corrosion resistance
Thanks to its chemical composition, Zamak is resistant to corrosion and ensures the durability of industrial plug socket-outlets, especially in environments where they may be exposed to humidity or corrosive chemicals.
-
Environment
Good resistance to petrol, alcohols, oils and mineral lubricants. Can withstand temperatures up to 200°C.
These characteristics make Zamak a suitable material for industrial plug socket-outlets, offering a combination of strength, longevity, ease of manufacture, and cost-effectiveness.
Copper-free aluminium
Aluminium is a material that allows great freedom in the design of parts, combining lightness, strength and resistance in all operating environments. The surface appearance depends on the casting and finish: anodising, paint, etc.
-
Lightweight
Aluminium is a lightweight material, making it easy to handle and install plug socket-outlets, especially in industrial environments where a lot of equipment may be moved or installed frequently.
-
Corrosion resistance
Aluminium has good corrosion resistance, which is important to ensure the longevity of plug socket-outlets, particularly in industrial environments where they may be exposed to humidity, chemicals or other corrosive agents.
-
Heat dissipation
Aluminium has good thermal conductivity, which means it can effectively dissipate the heat generated during plug socket-outlet use, helping to prevent overheating.
-
Ease of manufacture
Aluminium is relatively easy to shape and machine, making it easy to manufacture industrial plug socket-outlets with a variety of shapes and designs, to meet the specific needs of industrial applications.
Taking these characteristics into account, aluminium offers a combination of performance, longevity and cost-effectiveness. It can withstand temperatures of up to 400°C under certain conditions.
Contacts
The choice of contact material is fundamental. It must:
- Have the lowest possible contact resistance in order to avoid the release of heat and, a fortiori, deterioration of the contact
- Be sufficiently solid to offer a long time constant and high thermal inertia
- Maintain its electrical and mechanical properties for a long time, even in the event of accidental overheating, which could lead to accelerated oxidation (corrosion)
- Withstand electrical cut-off tests and the generation of electric arcs.

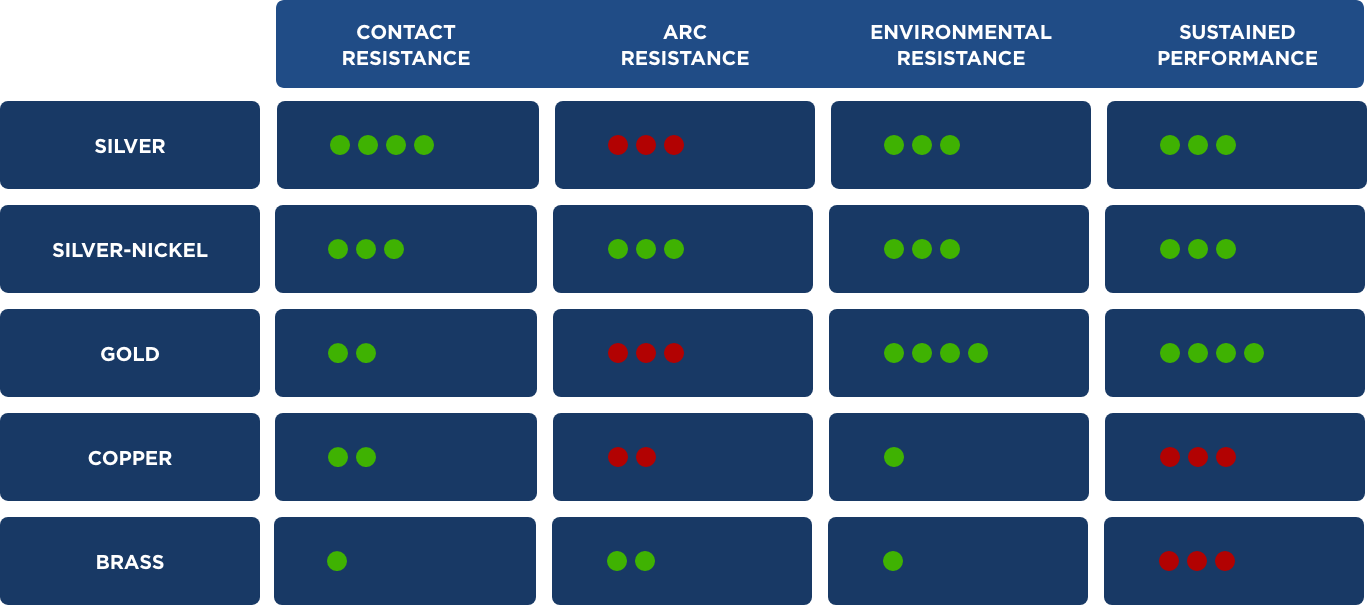
The material that best meets all the criteria is silver-nickel alloy. It is commonly used by all electrical switch manufacturers and has therefore been selected for DECONTACTOR™ to guarantee the best electrical conduction performance in operation and switching.
Screws and bolts
All our screws are made from stainless steel = a ferrous alloy containing more than 12% chromium.
This is a class of material with very good mechanical properties and resistance to a wide range of corrosive environments within extended temperature limits.